Heat Transfer Technologies for Combined Heat and Power Applications
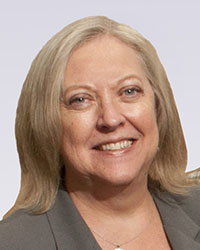
Patricia Irving
President/CEO
InnovaTek Inc.
ABSTRACT
Combined heat and power (CHP), also known as Cogeneration, is the concurrent production of electricity or mechanical power and useful thermal energy (heating, cooling, and/or process use) from a single energy input. CHP systems consist of a number of individual components—prime mover (heat engine), generator, heat recovery, and electrical interconnection— configured into an integrated whole.
CHP can operate in one of two ways: 1) Topping cycle – engines, turbines, microturbines, or fuel cells generate electricity and the waste heat is used for heating, cooling, and/or process use. 2) Bottoming cycle – waste heat from an industrial or other source with sufficiently high temperature is used to drive an electricity generator, frequently a steam turbine or organic Rankine cycle (ORC).
The efficiency of a CHP system is most commonly calculated by dividing the total usable energy output (electrical and thermal) by the total fuel input to the system. Today’s CHP systems are generally designed to meet the thermal demand of the energy user. CHP systems can achieve energy efficiencies of 75% or more compared to separate production of heat and power, which collectively averages about 50% system efficiency.
Thermal technologies used in CHP systems can be classified into three broad groups based on the application: 1) space conditioning, 2) domestic hot water or process heat, and 3) other industrial uses. Space conditioning can be further divided into cooling, heating, and dehumidification. The cooling technologies that are used in CHP systems are absorption chillers. Most CHP systems use hot water or steam generated in the heat recovery system directly for space heating. The dehumidification systems are either solid or liquid desiccant-based, with waste heat used for regeneration of the desiccant materials.
Reclaiming waste heat from the cooling system (often 30% of the total) is fairly straightforward. Heat from the engine’s exhaust gases (~ 40%) can also be reclaimed, but the gas-to-water or gas-to-air heat exchangers need to withstand the NOx and SOx held in the high temperature gases. Extracting all the heat means condensing the water vapor when it forms acids, which attack the exchanger (which also periodically needs to be cleaned of soot). Key design factors are the construction materials, temperatures and pressures, and water quality. Heat transfer rates depend on geometry and heat transfer area, coolant composition, coolant inlet temperature and flow rate.
Renewable CHP systems utilize biomass fuels. The industrial sector currently produces both thermal output and electricity from biomass in CHP facilities in the paper, chemical, wood products, and food processing industries. These industries are major users of biomass fuels—utilizing the heat and steam in their processes can improve energy efficiencies by more than 35 percent. In these applications, the typical CHP system configuration consists of a biomass-fired boiler whose steam is used to propel a steam turbine in addition to the extraction of steam or heat for process use, or chilled water for process cooling.
Fuel cell CHP installations using biogas can be used in commercial and institutional buildings where there is a relatively high coincident demand for electricity and thermal energy. Thermal energy recovered from fuel cells is most often used to satisfy hot water or space heating demands, although in some cases fuel cells have been integrated with absorption chillers to provide space cooling.