Low Temperature Waste Heat Recovery: Challenges and Opportunities
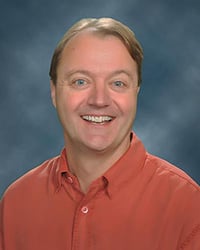
Thomas G. Lestina
Senior Vice President, Engineering
Heat Transfer Research, Inc.
EXTENDED ABSTRACT
Waste heat recovery has been used to reduce costs for energy intensive processes for decades. Although the design of heat transfer equipment and processes are well established, improvements have been gradual. Degradation in performance over time is expected and operating personnel remain focused on increasing product throughput rather than restoring/improving energy efficiency. Recent emphasis on sustainability in industry has changed the value calculation for energy efficiency for some processes. A review of standard practices, technology development, and new opportunities is warranted to establish a new standard and identify areas for investment.
Some waste heat can be recovered by preheating the feed stream. The design of the heat transfer equipment determines the preheating limit, taking into account temperature limits influenced by separation and reaction chemistry. Waste heat from flue gas and produced gas can be used to generate steam for facility heating and electric power generation. In general, steam is generated with gas streams greater than 250 °C. For air and water coolers, the waste heat is discharged to the environment without energy recovery.
To evaluate the possibilities for improvement, the principles of thermodynamics should be reviewed. Availability (or exergy) is the thermodynamic variable that gives a measure of the maximum amount of work that can be extracted from a system in a given surrounding. It is defined as

The availability is lower for streams near the surrounding temperature (often called dead state temperature). In a heat exchanger, the availability of the hot stream decreases and the availability of the cold stream increases. The magnitude of the change in availability is always less for the cold stream than for the hot stream. The second law efficiency of a single unit, two-stream heat exchanger can be defined as the increase in availability of the cold stream divided by the decrease in availability of the hot stream. This efficiency can be expressed as
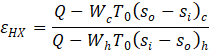
At flue gas temperatures greater than 250 °C, the efficiencies of waste heat recovery units are usually greater than 85%. For air coolers and water coolers, the efficiencies are less than 30%, indicating low value for waste heat.
Additional insight can be gained by expanding the study to consider an entire system (such as a Rankine or Brayton cycle). To realize large improvements in process system efficiency, multi-function process heat transfer systems should be considered. For example, the combined cycle power plants have efficiencies exceeding 60% by using the waste heat of the Brayton cycle to heat a Rankine cycle (whereas Rankine cycles alone have efficiencies of 33 – 40%). For fuel cell power plants, the efficiencies can approach 90% if a combined heat and power cycle (CHP) is used. By adding additional process functions, the control volume for the thermodynamic analysis is expanded to utilize the waste heat of the cold stream.
For low temperature applications such as cooling water and air cooling, waste heat is rarely utilized. While it is tempting to consider outlet cooling water and cooling air as a heat source, it is rarely done. Improving process efficiency with better heat transfer solutions may be more practical. For cooling water, reducing fouling and pressure drop are realistic goals to attain. For air coolers, reducing the fan power may be a cost-effective way to account for the duty removed.
The Horizon Symposium explores opportunities to improve waste heat recovery. New initiatives (e.g., thermal storage and carbon capture) are being commercialized, and innovative uses have been proposed. Efficiency improvements can be attained with advances in heat exchanger design. A sample of these technologies are presented at this meeting, including
- industrial heat pumps
- advanced absorption chillers
- heat recovery from produced water
- flue gas heat transfer
- feed/effluent process design improvements
Discussions should identify promising areas of investment to improve the technology.
Nomenclature
a, Thermodynamic availability, kJ/kg-K
h, Enthalpy, kJ/kg-K
Q, Duty, W
S, Entropy, kJ/kg-K
T0, Absolute temperature at dead state, K
W, Mass flow rate, Kg/s
eHX, Heat exchanger efficiency
Subscripts
i, Inlet
o, Outlet
0, Dead state